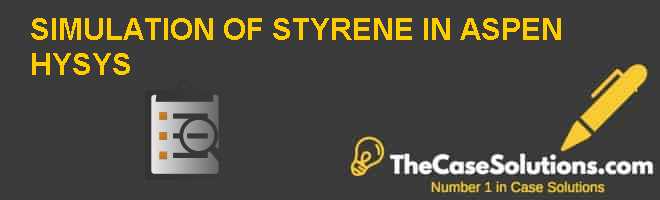
Simulation of Styrene In Aspen hysys Case Solution
Introduction:
Styrene is commonly known as ethylbenzene, phenyl ethane and vinylbenzene; it is an organic compound having chemical formula C6H5CH=CH2. This form of benzene is oily colorless liquid that has a sweet smell and is evaporated easily, but highly concentrated form of benzene has a pleasant odor. Styrene is ancestor to polystyrene and several copolymers.
Occurrence of styrene is very small in nature that means it’s very rare on the earth naturally, its major source are plants and foods. It is also found in coal tar.
The modern method to produce styrene is by dehydrogenation of ethyl benzene and was first done in 1930s.
As far as industrial production is concerned, Ethyl benzene is mixed with gas at a higher volume,which is probably high temperature steam and is passed through the catalyst, most of the times these catalysts are Iron oxide, potassium oxide or potassium carbonate.
Steam serves several other roles if we talk about this reaction, it follows the endothermic reaction. The other method to produce styrene commercially is given below:
Styrene can also be produced from toluene and methanol, which are cheaper than other available methods; it can also be generated with the help of carbon however,the issue with carbon generation is that the carbon might be an impetus poison. When potassium is mixed into the iron compound impurities occur, the impurities are cleaned (through the change of the response of carbon with steam to give primary gas, which is evacuated inside the reactor vent gas).
The operation of the operator and its conditions in modern reactors region reached to 620 °C and as low as practicable. The general result relies upon the relative measures of compound procedure change to vinyl ethyl and warm splitting to results. At balance beneath normal conditions, the reversible response winds up with respect to real change of ethyl radical sweet-smelling hydrocarbon. Be that as it may, time and temperature are important to accomplish as without maintaining the proper temperature and not doing it in time, then it could result in sudden warm breaking.
Problem Statement:
The aim of this simulation is regarding the optimization of styrene industrial production through chemical processes.For the production of styrene ethyl benzene, it is used by dehydrogenation process.This process uses ethyl benzene that is passed through recycled ethyl benzene, which is then heated and mixed with super heated steam. Steam here is to help the reaction like a catalyst does. The main purpose of this project is to optimize the equipment therefore,to achieve this purpose, the stream from the reactor is sent to the flash tank and after that the stream is sent to the decanter and finally, the residual stream contains the ethyl benzene.
Methodology:
The method which we have used in the optimization of the problem is very simple and easy to use for the separation process, as well as it is more important to choose the software for simulation and we have used ASPEN Hysys version 3.2 for this. Moreover, for the optimization of problem the order of separation is necessary. In addition, for the base, benzene and toluene were used and were separated in the distillate whereas, the bottom remained filled with styrene and ethyl benzene. Now what we need is to separate both these from each other and in order to do this,we have to send the residual chemicals to another distillation process.
Initially, we used the mixer to mix all the chemicals and after that a pump was used as it can be seen in the figure below; after that another mixer was used to mix the steam and all the chemicals. Moreover, two plug flow reactors were used and connected with each other proceeding it we used cooler to cool down the process and chemicals as we previously used super-heated steam so we cooled it.After using three phase separator, we will get the styrene..........................
This is just a sample partial case solution. Please place the order on the website to order your own originally done case solution.